NCAME cultivates additive manufacturing vendor partnerships for NASA
Published: Sep 14, 2020 8:00 AM
By Jeremy Henderson
Inside a state-of-the art 50,000-square foot South Dakota facility, within view of Mount Rushmore, one of the largest examples of subtractive manufacturing in the world, sits one of the world's largest additive manufacturing machines, or 3D printers for metal parts.
"The 557XR is for blown powder laser directed energy deposition (DED)," said Nick Wald, general manager of RPMI, the pioneering Rapid City-based additive manufacturing (AM) company behind the massive professional grade system. "It's a big machine."
And, thanks to the latest developments in Auburn University's public-private partnership with NASA, it's got a big job to do.
RPM Innovations (RPMI) is one of several leading specialized technology vendors in a domestic advanced manufacturing supply chain cultivated by Auburn University's National Center for Additive Manufacturing Excellence (NCAME). The supply chain is integral to a growing AM research and development contract from NASA for improving the performance of the liquid rocket engines that will return astronauts to the moon and beyond.
Titled Rapid Analysis and Manufacturing Propulsion Technology (RAMPT), the project aims to evolve light-weight, large-scale novel AM techniques like DED — RPMI's specialty.
“RAMPT aims to develop and advance new manufacturing technology, with the primary application being a large-scale thrust chamber assembly for liquid rocket engines,” said RAMPT co-principal investigator Paul Gradl, a senior propulsion engineer at NASA’s Marshall Space Flight Center in Huntsville. “This large-scale demonstrator nozzle is critical to demonstrate the technology’s potential and to spur innovation in small commercial businesses in the industry. It’s a forward-thinking public-private partnership.”
RPMI recently used the 557XR's DED capabilities to produce one of the largest integrated-channel rocket nozzles ever printed. Measuring 40 inches in diameter and standing 38 inches tall, the nozzle features hundreds of internal coolant channels, and was built in only 30 days — a year ahead of schedule — thanks to RPMI's success with the new fabrication process.
“New large-scale technologies like laser beam directed energy deposition can produce components much more efficiently in low-volume production than traditional engine nozzle fabrication methods,” said NCAME director Nima Shamsaei, Auburn’s technical lead for the RAMPT project. “At the same time, they can also deliver very complex parts, including engine nozzles with internal coolant channels.”
But it's one thing to deliver them. Perfecting them is a different ballgame.
"Due to the very unique thermal history that parts experience during additive manufacturing, their microstructure often differs from their conventionally-manufactured counterparts,” Shamsaei said. “Therefore, there is a critical need for new materials data to evaluate and qualify the performance of the additively manufactured parts. At NCAME, we test and characterize the materials that are used in the fabrication of these parts, and more importantly, make the data publicly available for a broader industrial use."
NCAME associate director Mike Ogles, Auburn’s RAMPT project manager, agrees.
“RPMI's cutting-edge technology and NCAME’s expertise in materials characterization and qualification will help further accelerate the use of additive manufacturing technologies in the aerospace sector,” Ogles said.
Media Contact: , jdh0123@auburn.edu, 334-844-3591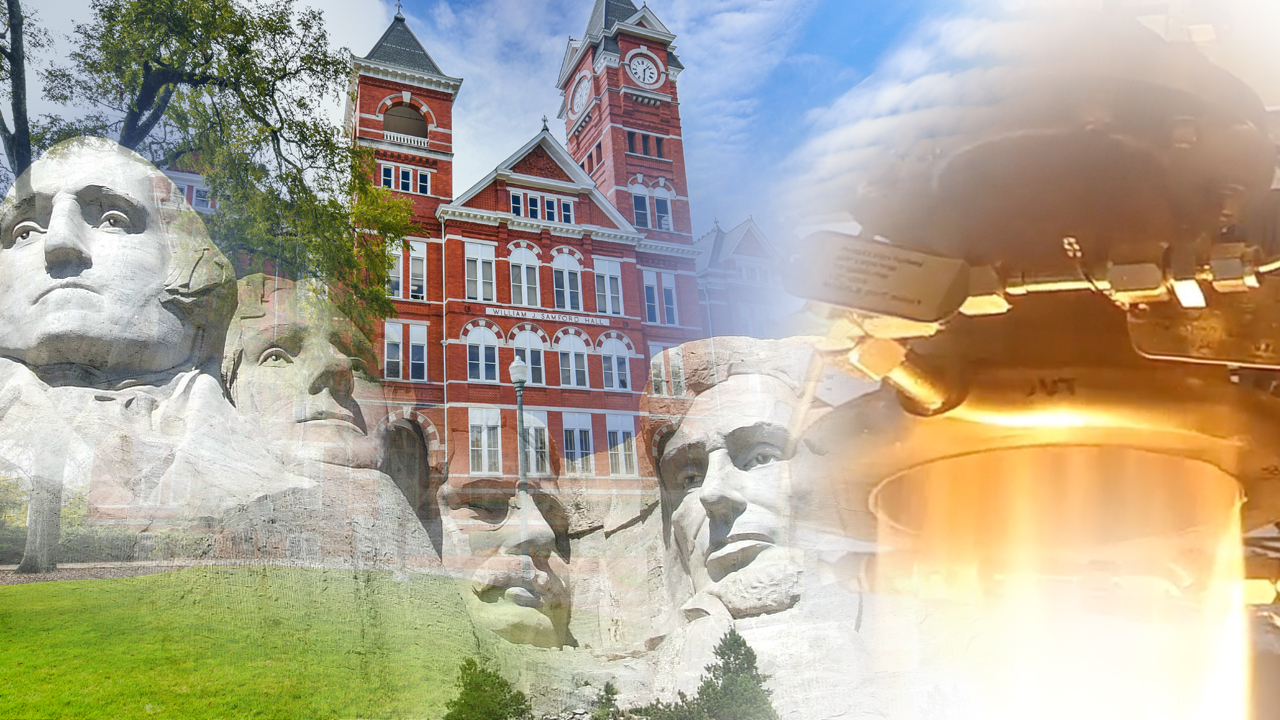
Rapid City-based RPM Innovations is one of several leading specialized technology vendors in a domestic advanced manufacturing supply chain cultivated by NCAME.